Wear Parts Application
Wear Parts Application: A Crucial Component for Durability and Performance
In industries like mining, construction, agriculture, and manufacturing, wear parts are essential for ensuring the longevity and efficiency of machinery and equipment. These parts, designed to withstand constant friction, pressure, and abrasive wear, are integral to reducing downtime, improving productivity, and maintaining optimal performance. In this blog, we’ll delve into the importance of wear parts, their applications, and how they contribute to various industries.
What Are Wear Parts?
Wear parts are components of machinery and equipment that are subject to wear and tear due to friction, abrasion, and corrosion during operation. These parts are designed to be replaced after they have degraded over time. Common examples of wear parts include cutting blades, conveyor belts, hammers, liners, and seals. The materials used for wear parts are typically harder or more resistant than the equipment they are used with, to prolong the lifespan of the machine and reduce the frequency of repairs.
The Importance of Wear Parts
1. Minimizing Downtime
The most significant advantage of wear parts is the reduction in equipment downtime. When wear parts degrade or break down, the entire machine or system can stop functioning. This interruption can lead to costly repairs, production delays, and lost revenue. By regularly replacing wear parts before they wear out completely, industries can keep operations running smoothly and avoid unexpected breakdowns.
2. Improving Efficiency
Wear parts help maintain the overall efficiency of the machinery. Over time, worn-out parts can cause machines to operate less effectively, increasing energy consumption, or causing delays. Using high-quality, durable wear parts ensures that machines continue to operate at peak performance, reducing waste and energy costs.
2.Safety
Worn-out parts can lead to malfunctioning equipment, which in turn can pose serious safety risks. Wear parts, like brakes and seals, are essential for safe operations in industries such as mining and construction. Regularly replacing these parts helps to maintain safe working environments for operators and prevents accidents caused by malfunctioning machinery.

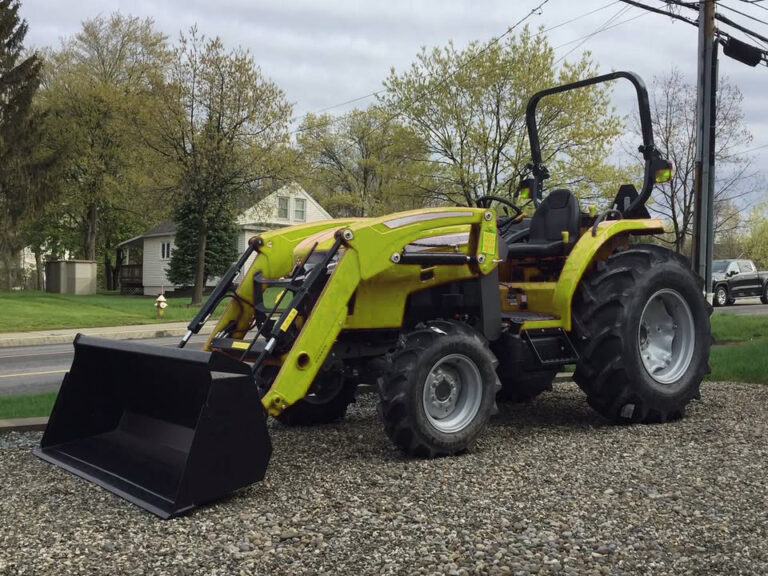
Wear Parts Applications Across Industries
1.Mining
In mining operations, machinery and equipment are constantly exposed to harsh conditions, including high impact, abrasive materials, and extreme temperatures. Wear parts like crusher liners, bucket teeth, and conveyor belts are essential for maintaining productivity and reducing operational costs. Mining equipment such as excavators, drills, and loaders depend heavily on wear parts for efficient material handling and excavation.
2.Construction
Construction machinery, such as bulldozers, backhoes, and excavators, operates under heavy-duty conditions, often on rough terrains. Wear parts in these applications include bucket teeth, wear plates, cutting edges, and hydraulic seals. These parts ensure that construction equipment can handle tough materials like concrete, asphalt, and rock without breaking down prematurely.
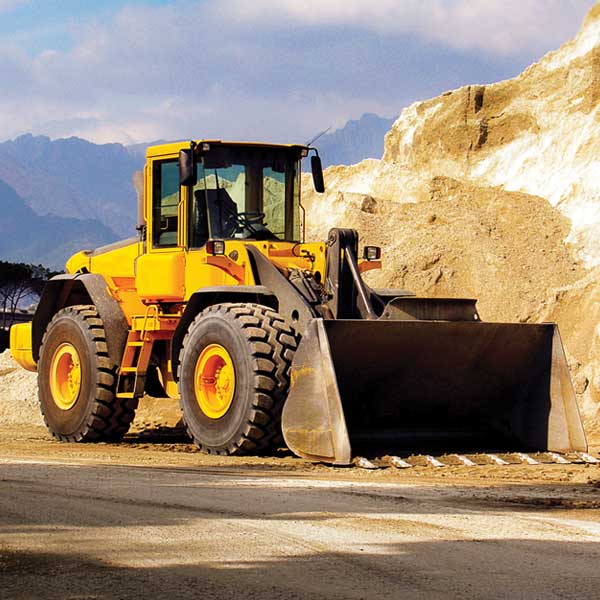
3.Agriculture
In the agricultural industry, wear parts are commonly used in harvesting equipment, tractors, and tilling machinery. Parts such as blades, discs, and belts are exposed to dirt, debris, and hard soil, all of which contribute to the wear. Regular replacement of these components ensures smooth operations during planting and harvesting seasons, minimizing downtime and maintaining the efficiency of the machinery.
4.Manufacturing
Manufacturing industries rely on wear parts for machinery such as presses, mills, and automated systems. Parts like molds, dies, and bearings wear down after repeated use, impacting production rates and quality. By replacing these wear parts regularly, manufacturers can maintain the consistency and precision of their operations, which is crucial for delivering high-quality products.
Material Selection for Wear Parts
The material selection for wear parts is critical in determining their durability and performance. Common materials used for wear parts include:
- High-carbon steel: Known for its hardness and wear resistance, high-carbon steel is often used in wear parts for heavy machinery.
- Alloy steels: Alloys with added elements such as chromium or molybdenum can improve wear resistance and toughness, making them suitable for high-impact applications.
- Ceramics and composites: These materials offer exceptional wear resistance in applications that deal with extreme temperatures and corrosion.
- Hardfacing: A process where a hard, wear-resistant material is applied to the surface of a part, extending its lifespan in abrasive conditions.
The right material depends on the specific application, the type of wear (abrasion, impact, corrosion), and environmental factors.
Conclusion
Wear parts play a crucial role in the longevity, performance, and efficiency of machinery across a wide range of industries. By ensuring the regular replacement of these components, companies can minimize downtime, enhance productivity, and improve safety. As industries continue to evolve and machinery becomes more specialized, the demand for high-quality, durable wear parts will only grow.
Investing in quality wear parts is an investment in the long-term success of operations. By choosing the right materials and regularly maintaining these components, businesses can maximize the lifespan of their equipment and maintain peak performance throughout the lifecycle of their machinery.
Contact Us Today!
Partner with industry-leading precision casting experts to bring your vision to life. We specialize in delivering custom, high-quality casting solutions. With years of experience, cutting-edge technology, and an unwavering commitment to excellence, we ensure every component exceeds your expectations.
